FOAMSCAN™
Foam Analyzers and Defoamer Testers
FOAMSCAN™ the most accurate Foam analyzer for your Laboratory.
Liquid foams are ubiquitous in various industrial processes and in our everyday lives. Being able to generate a controlled liquid foam and understanding the phenomena responsible of its destabilization is hence crucial to optimize formulations.
Foaming and stability properties depend on:
-
Liquid Fraction: liquid quantity compared to foam volume
-
Size of bubbles: from micrometer to centimeter
-
Polydispersity: distribution of bubble sizes
TECLIS range of Foam Analyzers characterizes precisely foaming properties and test defoamers effectiveness saving valuable time in foaming products formulating.
FOAMSCAN™ Foam Analyzer
foam generation methods
Several methods can be used to generate a liquid foam
-
Injecting a gas into a liquid phase through a porous media
-
Mechanical stirring, such as mixer, shaker..
-
industrial devices such as spray can, effervescent tablet, chemical reaction.
Energy input is required but not sufficient, Surfactants play a key role on the foamability of a solution.
Multi-scale image analysis software
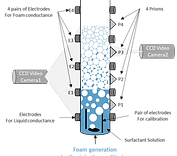
FOAMSCAN Software:
-
measures precisely the volume of foam.
-
Liquid fraction and volume are determined in real time from the conductivity electrodes.
-
controls measurement parameters: Gas flow rate, stirring speed
-
Cell Size Analysis software measures bubbles 'size and distribution.
Full range of Measurements
All along the experiment
-
Volume of foam / liquid
-
Liquid fraction (Drainage)
-
Foam Density / Stability
-
Bubbles Size and distribution

During the foam formation
-
Capacity of Foam
-
Bikerman index
Since end of foaming
-
Capacity of Foam
-
Index Bikerman
-
Expansion coefficient
-
Conductance
-
Foam maximum density
-
Foam stability index
For Lots of Applications...
Crude oil: Foamability by gas injection and depressurization, defoamer testing.
Cosmetics: foam texture depending on liquid fraction and bubble size, foam stability.
Sodas, beer, Champagne: control of foam by depressurization or when pouring a glass.
Environment: Foam study for material extraction from soil, decontaminating foam study.
Chemistry: Anti-Foam for manufacturing products, detergents, solid foam properties (cement).
FOAMSCAN™ - Foam generation by Gas Injection
The Foamscan is designed to characterize foam properties (generation and stability). Foam is generated by injecting some gas (Air, N₂, O₂, CO₂...) through the liquid.
The software controls the gas flow rate and the foam volume is determined in real time by image analysis using a CCD camera. Liquid fraction and volume are determined in real time with the conductivity electrodes. CSA software analyses the size and distribution of the bubbles.
The measuring tube is chosen depending on the applications that are studied:
-
equipped with conductivity electrodes to measure the liquid fraction of aqueous foams in real time
-
with a double glass wall to control the temperature up to 90 °C during experiment ( with optional circulating bath)
-
equipped with 4 prisms to adapt to the Cell Size Analysis (CSA) option
Applications
-
Foamability: shampoo, cream, coffee, beer, additives, formulation etc...
-
Scientific correlation with sensorial test
-
Improve formula and surfactants' screening
-
Foams for cleaning and detergents
-
Firefighting foams
-
Sparkling products
-
Flotation as a method for separating solids
-
Foam-reducing agents
Options
-
Size of the bubbles (CSA)












FOAMSCAN™ - Foam generation by mechanical Stirring
This instrument measures the ability of a liquid to generate foam by mechanical stirring. A set of rotating blades produces foam under the control of the software. The maximum rotation speed is 6 000RPM, and depends on the viscosity of the product.
The software controls the stirring rate and the foam volume is determined in real time by image analysis using a CCD camera. Liquid fraction and volume are determined in real time with the conductivity electrodes. CSA software analyses the size and distribution of the bubbles.
Both foam generation by sparging and by mechanical stirring can be combined in the instrument.
Applications
-
Foamability: shampoo, cream, wine, beer, additives, formulation etc...
-
Scientific correlation with sensorial test
-
Improve formula and screening surfactant
-
Foam generates with shear
Options
-
Bubbles size and distribution analysis (CSA)












JETSCAN™ - Foam generation by Jet circulation / defoamer Tester

JETSCAN™ has been designed to measure efficiency and persistence of anti-foam agents on foams produced by liquid jet circulation. It uses image analysis techniques combined with TECLIS software to control each measurement and acquire data.

The Protocol has been designed to measure how efficient and persistent a defoamer is

Up to 28 samples tested automatically

JETSCAN™ has been designed to measure efficiency and persistence of anti-foam agents on foams produced by liquid jet circulation. It uses image analysis techniques combined with TECLIS software to control each measurement and acquire data.
Applications
-
Food and beverage production, processing and packaging
-
Laundry Detergent Manufacturing
-
Home & personal care
-
Beers, sodas dispensers
-
Biomaterials and Paper products
-
Antifoams & Defoamers effectiveness
-
Foam prevention for paints and varnishes
-
Wasted water process
Options
-
Automatic Cleaning
-
Automated antifoam injection
-
Automated sampler
JETSCAN™ has been designed to measure defoaming agents' efficiency and persistence on foams produced by liquid jet circulation, using image analysis technics combined with TECLIS software.
Fully automated, JETSCAN™ controls experiment parameters, collects and injects up to 28 defoamer samples, measures foam volumes, clean the whole system after testing which gives the JETSCAN™ a high added-value in high-through-put defoamer testing.